May 2016 - November 2016. Dangerous throttle cable problems.
The problem -
When high revs were demanded, e.g. moving away on a roundabout, a road junction or steep hills, the engine would
suddenly go to (almost) full throttle. This was very dangerous if you don't know what to do. The brakes can't fight
the engine. The engine goes to high revs and the vehicle tries to accelerate out of control. You must realise straight
away what is happening and turn off the ignition. Turning off the engine can still be dangerous in traffic and as you
move out of junctions etc. Pulling over and inspecting the engine showed the problem was a "snagged" throttle cable.
This problem lasted for months as various solutions were tried and then failed. In order to solve a problem it is very
important to first of all understand what was causing it. When you read this account it will all sound obvious but, just
like an illusion / magic artist it is easy once it has been explained. Let's start with what happened and how the
thought processes resulted in solutions which, at first, failed. At this early stage the underlying problem which
caused the failures was not understood.
The first throttle cable -
Major upgrades had been done to the truck through the winter of 2015 and into the Spring of 2016. Many engine mods.
had been done through 2015 but the truck had not been tested. It was then prepared for paint, painted and the
upholstery etc. all done without a break. From the end of May 2016 testing started and teething troubles dealt with
after the many mods. most problems were sorted apart from one which kept coming back. The throttle cable snagging
and almost going to full throttle until the engine was turned off. Looking at the picture below you can see the
first throttle cable. It was fitted early in 2015 after the new carburettor was fitted. In May 2016 it failed.
This was a "Lokar black PVC outer" type throttle cable. These cables are universal fit and need to be cut to length.
The firewall end is bonded to the fitting and the carb. bracket end is loose. There is a metal cap pushes over the
end of the PVC and this loosely inserts into the fitting. It is held into the fitting by making sure the cable is
cut to the correct length and flexing it between the two end stops which are the firewall and the carb bracket.
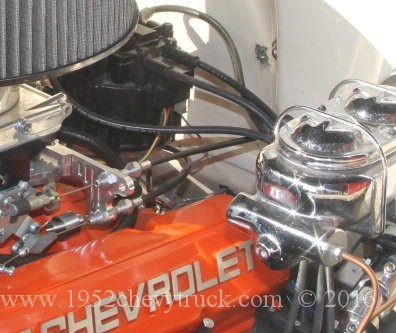
Also note the cable is not exactly straight but it is almost straight. When the problem described actually happened
for the first time, the engine was inspected and nothing could be seen to indicate what had gone wrong.
The cable looked perfect and the truck started up again as normal.
Eventually after it had happened two or three times, inspection showed the throttle cable end had jumped out of the
end holder (at the carb end) and was snagged at an angle resulting in an open throttle situation. What had happened
before that discovery was the cable had freed itself and jumped back into the end fitting which is why at first it
was puzzling as it looked normal. The third time it stayed out of the fitting and it was possible to take hold of
it and flex it back in. Then it was possible to carefully drive home. If this is difficult to follow, further
pictures below will help explain how the cable snagged in the carb bracket end fitting. When it snagged it pulled
the throttle to a wide open position. The throttle pedal stayed down as the cable was jammed open.
The second throttle cable -
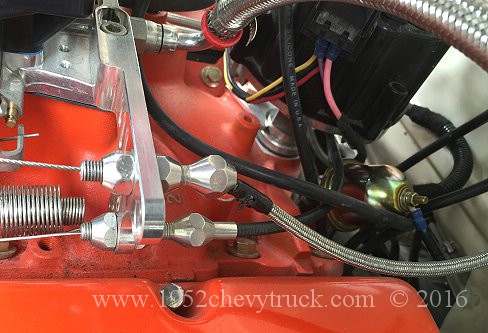
The picture top right above shows how one end failed. This was the second throttle cable. After the first one failed
it was decided the problem was due to the cable not being flexible enough. The black PVC was stiff and a more flexible
Locar stainless steel braided cable was purchased. This cable also pulled out at high revs and failed with the same
dangerous results. Since the underlying reason at this stage was still not understood a new incorrect decision was
made but first another throttle cable was purchased. Another Lokar stainless steel braided. The incorrect assessment
resulted in treating the problem and not the cause of the problem, it was decided both ends needed to be bonded
so that one at the carb end could not pull out! Simple but wrong. See throttle cable 3 below. The two pictures
directly below show the cable before it failed. Notice it has been bonded to the fitting.
The third throttle cable -
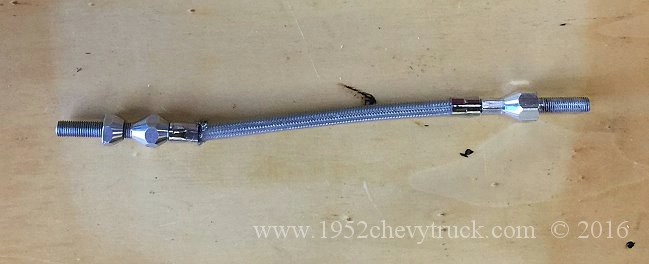
The third (new) cable above was sent to a specialist company in the UK called
Venhill Engineering. They did an
excellent job. The loose end which went into the fitting at the caburetor bracket was bonded. In addition, the
cable was strengthened along it's length with a clear outer cover. It is difficult to see this clear cover in the
pictures but it is there. It is a bit like the clear tubing used on aquariums but thinner walled and close fitting.
This cable was immensely strong and bonded at both ends. It made no difference at all. It still failed. Time for a
re-think! The underlying reason needed to be understood. Up until this point only the force of the foot on the
pedal and the force of the return spring had been considered. Something else was going on.
It now became clear that the strength of the cable was not the issue as the forces involved to make it fail must have
been massive. A bit of Physics was needed to work this out. Clearly the reason the throttle cable was pulling apart
was because the distance between the carburettor bracket and the firewall was increasing at high revs. When an engine
is at high revs it has a turning moment. The crank shaft turns in one direction of rotation and so the engine reacts
to that and moves. This massive force of the engine moving increases the gap between the carb bracket and the
firewall and the throttle cable pulls apart as there is no "give" in the cable to allow for this movement.
A short throttle cable has virtually no "give".
The forth throttle cable -
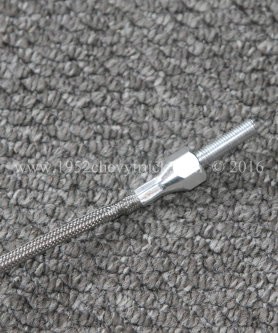
The 4th throttle cable was made by "So Cal" and was half the price of the Lokar unit. Again it was stainless steel braided.
This was 36 inches long and the plan was to try a giant horizontal loop around the distributer. It emerged from the
firewall, went round the distributor, and back to the carb bracket. The theory being that a loop would provide "give"
and compensate for engine movement. The new cable was fitted but when tested (without starting the engine) by
pressing the pedal there were two problems. The first was the cable "kinked" where it emerged from the firewall.
This was caused by the force of the pedal pushing against the carburator return spring and by the way the cable
was routed. The second problem was that since this make of cable was more flexible and not as strongly made,
the kinking and the compress-ability meant the movement back and forwards at the carb bracket was less for the
same amount of pedal movement. Also the kink was permanent making the cable now useless. This exercise showed
that whilst a loop might be a good idea, the cable needed to be strong, incompressible and flexible.
The fifth and final throttle cable -
There were therefore three requirements in the solution. A strong throttle cable bonded at both ends but also with "give".
It was decided the best way to achieve that was with a new vertical loop as shown in throttle cable 5 below.
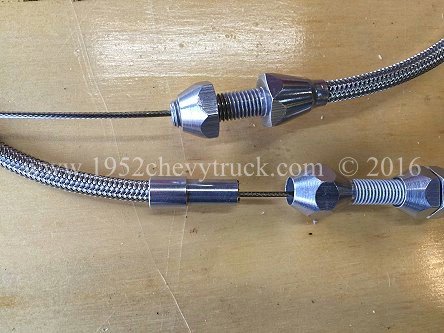
The pictures above show the new 24-inch
Lokar throttle cable. These
pictures show it when new and not bonded or
strengthened. It was sent to
Venhill Engineering to have the ends bonded and for the clear strengthening cover to
be fitted. It was returned and fitted. Again it is difficult below to see the clear strengthening cover but it is there.
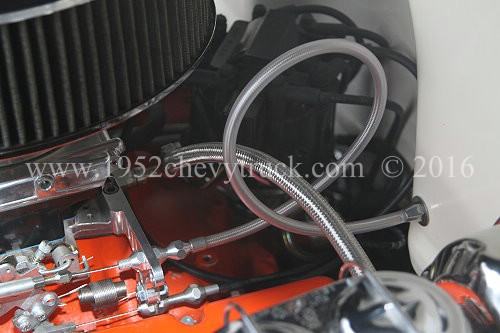
It has taken a while to solve this problem and it may seem to be an obvious solution now this has all been
explained or maybe many people out there have seen this before. Hopefully these notes will help others. The
final solution is strong, it has "give" to adjust for engine movement and it still looks very good.
(The cause of this throttle cable problem is found. See below.)
Costs -
The Lokar stainless steel throttle cables (x3) are about £40.00 ($55) each,
The Lokar black PVC cable (x1) was about £30.00 ($38.00) and the So Cal cable (x1) was about £20.00 ($25)
The work done by Venhill Engineering (x2) was about £40.00 ($55)
The time taken to sort this out was considerable, however, these costs are not really important when
a major safety problem has been solved.
Carburetor notes. -
Notes on fitting and setting up the Street Demon carburetor can be found in several places on this site.
1. Fitting the carburetor -
fitting.
2. Setting up the TV Dent cable.-
TV cable.
3. Monitoring the transmission oil pressure -
pressure gauge.
3. Fitting a throttle return spring -
return spring.
4. Throttle cable and the need for a loop -
Loop.
Note - British spelling - carburettor. American spelling - carburetor.
Feb. 2019. The cause of the throttle cable problem is found -
(These notes refer to the problem above)
In Feb. - March 2019 the engine was pulled out as part of a major
"isf" upgrade. A broken engine mount
was discovered. When accelerating hard, the engine must have been moving (rotating) and causing the
throttle cable to break leaving the throttle wide open and the engine surging. It was realised that the
type of engine mount used, a very common type, has the disadvantage of being hidden. Therefore
inspecting that type of engine mount is not possible without lifting out the engine.
See this common "hidden" type of engine mount in the pictures below.
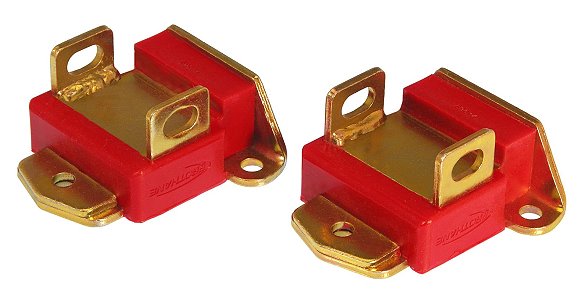
A much better engine mount was fitted. See pictures below. Here it is very easy to inspect the mount. It was
decided to keep the throttle cable loop as this maintained flexible isolation between the engine and the cab.
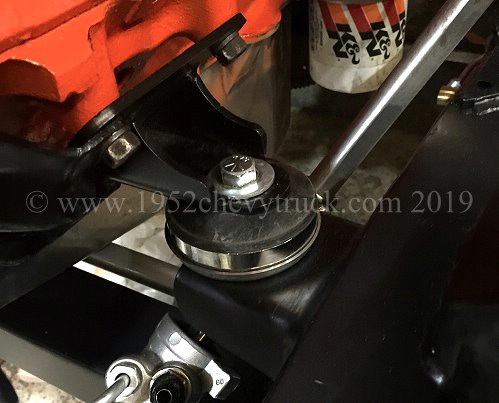
These engine mounts are available from "
Highway Hell hotrods" in the UK.